Gianfranco Conti, Emerson’s regional sales manager for Latin America, and Lyndon Dean, Emerson’s business development manager for Australia/New Zealand, recently published an article in the April 2023 issue of Global Mining Review on pages 27-30. It is titled “An Electric Alternative” and it describes how advances in functionality and performance are making electric actuators the preferred alternative in many mining applications. The article is summarized below.
An increasing focus on decarbonization and sustainable commerce across the world is driving a transition to electric vehicles, increased green energy production, and more efficient electrical devices. These trends are creating burgeoning demands for lithium and other rare earth metals, spurring significant mine expansion. However, those same environmental, social, and governance (ESG) trends are also being applied to mining operations, forcing the industry to improve its own ESG efforts.
Valve actuation decisions
Automated valves are critical in mining and ore processing. Historically, hydraulic valves have been utilized for high-pressure applications, and pneumatic valves have been used for nearly everything else. Traditionally electric valves were underutilized due to their limited torque and lack of a fail-safe response on power loss, but pneumatic valves also have their issues. They require a source of high-quality air, which can be difficult to supply in remote applications. They also tend to be less reliable than electric actuators in the long term, especially if the quality of the air is not carefully monitored and maintained.
Recent improvements in electric actuation technology are changing the valve actuation landscape in mining applications (Figure 1). Electric actuators can now meet the torque and stroke speed requirements for most applications, and they can even fail to a safe position on loss of power.
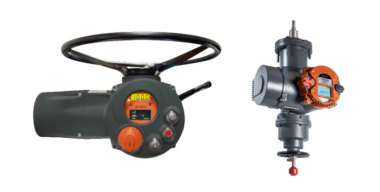
Figure 1: Emerson’s next generation Emerson’s Bettis XTE3000 Electric Actuator (left) provides up to SIL 3 reliability, programmable stroke profiles, and advanced diagnostics. The Bettis RTS actuator (right) can fail open or closed on loss of power using a mechanical spring, provide continuous modulation, and achieve SIL 3 reliability.
The authors describe the impact of these advancements on valve actuator selection:
While electric actuators can be more expensive initially for some applications, they tend to cost less when one considers the operational cost of the air system itself, along with the pneumatic actuator expense. Electric actuators also tend to have better reliability in the long term, requiring less maintenance and repair.
Which actuator is best?
Like any other technology, both pneumatic actuators and electric actuators have their advantages and disadvantages (Figure 2).
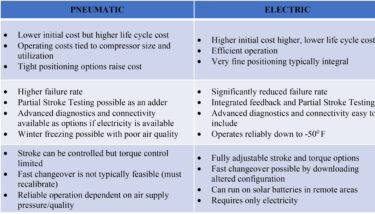
Figure 2: Significant recent advances in electric actuator functionality and performance have altered the economic landscape for valve actuation selection.
Pneumatic actuators may cost less initially, but they tend to become less reliable over time. Their overall efficiency is tied directly to the sizing and operation of the air compressor itself. An oversized or poorly maintained compressed air system will result in very high operating costs. Pneumatic actuators tend to be smaller for a given torque size, but are not inherently good at positioning, requiring expensive positioners to achieve tight valve position control.
Design enhancements have made electric actuators more competitive and efficient. They may cost more initially, but over time their improved reliability, and independence from an air system, make them less expensive to operate. Very precise positioning and advanced torque control are usually part of the actuation package, allowing the valve to execute any number of positioning and torque profiles. Recent electric actuator designs incorporate spring return electric fail-safe capability, achieving SIL 3 safety shutdown ratings, while providing a predictable response should power be lost.
Picking the right option
The best technology often depends upon the relative size of the valve and the existence of a compressed air system. If a pressurized air system already exists, adding a few more pneumatic valves to it is likely the best choice. In a greenfield application, an all-electric actuation solution may be better option, particularly when the capital and operational cost of a new compressed air system is considered. Other drivers impacting the decision include a requirement for variable stroke/torque profiles or precise positioning, the ability to power actuators with solar power, or water-constrained environments, which raise air compressor operating costs significantly.
Electric valves in mining service
Mining operators are starting to use electric actuators in a variety of applications:
- Solar-powered valve actuators control water truck filling in remote locations.
- Some countries require new mines to provide their own water supply, so many mining operators are installing desalination plants. The dusty, salt laden environment makes the operation and maintenance of an air system cost prohibitive, driving companies to use electric valves instead.
- In a bid to go carbon neutral by 2030, a mining company is employing electric valves as part of a sitewide initiative. The advanced diagnostics and higher efficiency of the electric actuators are expected to reduce energy utilization, while significantly cutting operating costs.
The authors conclude with these thoughts:
Recent design advances have provided improved reliability and functionality, altering the decision landscape for pneumatic versus electric actuators. While the ultimate decision will depend upon the existing infrastructure and specific application, electrically actuated valves are increasingly becoming a financially superior option for many mining applications.
Visit the Bettis XTE3000 Electric Actuator page on Emerson.com for more on this technology and how it can help enable safer and more reliable operations.
All figures courtesy of Emerson