Across many process manufacturing and producing industries, falling prices are driving the need for increased efficiency and reliability, as well as reduced costs. While optimizing process control can yield gains, so can applying technology to the condition of the equipment involved in process operations.
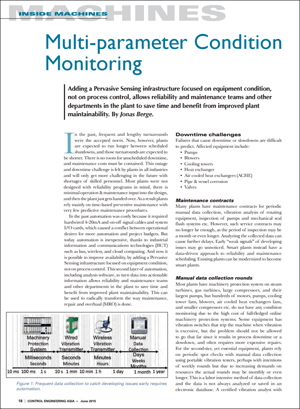
Making this possible is the availability of:
…industrial information and communications technologies (IICT) such as bus, wireless, and cloud computing.
Jonas lists typical pieces of equipment that can lead to unplanned downtime and process slowdowns:
- Pumps
- Blowers
- Cooling towers
- Heat exchanger
- Air cooled heat exchangers (ACHE)
- Pipe & vessel corrosion
- Valves
He describes the shortcomings in maintenance contracts for manual periodic data collection, rotating equipment vibration analysis, pump seal flush systems, etc. The lag between inspections may allow problems to develop and worsen. A better approach is to have:
…a data-driven approach to reliability and maintenance scheduling. Existing plants can be modernized to become smart plants.
For plant assets not already protected with continuous protection and prediction monitoring, the:
…wireless vibration transmitter is another way to monitor vibration on non-critical rotating equipment, serving as an intermediate tool to complement online machinery protection systems and portable vibration testers.
Many essential assets such as cooling tower fans, air-cooled heat exchangers, and blowers to name a few are not easily monitored due to safety concerns and access difficulty. For these applications, the:
…vibration sensors are mounted inside the enclosures and wired to the wireless transmitter outside the enclosure.
Instead of collecting data from manual rounds on a weekly, monthly or quarterly basis, more frequent [hyperlink added]:
…data automatically monitored by software improves the data analysis to capture developing issues in the early stages rather than later, when damage or outright failure and shutdown have already occurred. More frequent and recent data makes the diagnostics more predictive, makes root-cause analysis easier, and also makes it possible to visualize degrading conditions by severity trend in software.
Jonas describes how diagnostics such as PeakVue Analysis, provide early warning to impending problems in time to take proactive actions to address the problem before a failure occurs.
He describes multi-parameter condition monitoring as being about:
…observing measurable properties for signs of internal fouling or faults. Additional sensors for equipment pressures, temperature, flow, auxiliary seal flush fluid levels, position, pH and conductivity provide data on operating process and ambient conditions that help in root-cause analysis. This allows other problems like fouling, scaling, and leaks etc. to be detected.
You’ll want to read the article for examples of how multi-condition monitoring is applied to air-cooled heat exchangers and pumps to improve overall reliability and efficiency of maintenance operations.
You can also connect and interact with other reliability and maintenance experts in the Reliability & Maintenance group in the Emerson Exchange 365 community.