Storage tanks can safely hold thousands of barrels of product, but they are sensitive to overpressure and vacuum conditions, which can lead to product loss or excess emissions. Our article in the March 2025 issue of Valve World, titled “Hazardous storage tank pressure protection and emissions control,” discusses protective equipment that promotes operational safety while minimizing environmental impact, even in storage tanks containing hazardous volatile organic compounds.
Pressure and emissions challenges
The focus here is only on low-pressure storage tanks holding liquids that are stable at room temperature. In these tanks, keeping internal pressure within vacuum and pressure design limits is critical.
Many storage tanks can sustain a vacuum of only a few inches of water, and the maximum pressure may be one PSI or less.
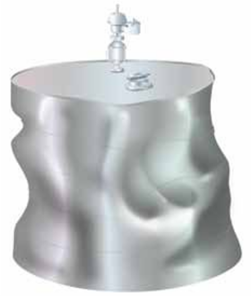
It does not take much pressure or vacuum to damage or even destroy a typical storage tank
Additionally, volatile organic compound emissions must be kept low to comply with Environmental Protection Agency and other regulatory requirements.
Multi-layer pressure control
Tanks naturally and continuously breathe in and out due to changing operating and environmental conditions. In general, they develop a vacuum when material is pumped out of the tank or when ambient temperature drops. Conversely, they develop excess pressure when material is pumped in, when ambient temperature rises, when fires occur near the tank, and possibly in other scenarios, depending on tank contents and surrounding equipment.
In normal conditions, a slight positive pressure is maintained using a blanketing regulator and a scrubber/vapour recovery/flare system. A vacuum/pressure vent acts as a second layer of protection, pulling in or venting air directly to atmosphere if necessary. Finally, a large emergency vent protects the tank from vapour loads caused by extreme events, like a nearby fire.
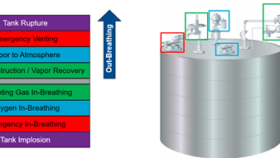
Tank pressure controls require a variety of devices that operate to keep the tank pressure neutral (green zone). Pressure protection is provided in layers, with each device coming into operation as pressure or vacuum changes in the tank vapour space
Equipment details
Tank blanketing regulators add an inert gas, such as nitrogen, to maintain a slight positive pressure and prevent oxygen from entering the tank. Key design features include very tight pressure control at low flow, and no leakage to reduce inert gas usage.
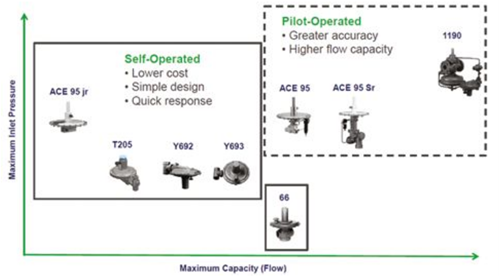
There are a variety of tank blanketing regulator designs available to handle varying incoming gas pressure and flow capacities (Emerson’s Fisher blanketing regulators shown). Very tight pressure control at low flow and fast speed of response are key features
Vapour recovery regulators handle excess pressure by venting tank vapours to a scrubber, vapour recovery system, or a flare so they can be processed in an environmentally friendly manner. These systems require precise control at low pressures, along with tight shutoff when not in operation.
Tank pressure/vacuum vents should only come into operation during atypical conditions where the required flow rates exceed that of the blanketing and vapour recovery regulators.
These vents must operate reliably despite months or even years of inactivity, and they must have near-zero leakage closed.
Ideally, an emergency tank vent should never come into service, but if an abnormal fire or pressure event occurs, the vent will relieve the vapour load to protect the tank.
These devices use a weighted lever assembly that opens within a tight tolerance of the set pressure, and they require very low leakage, usually less than one SCFH at 90% of the pressure setpoint.
Reliable protection
When developing a tank safety system, design professionals are advised to consult with tank pressure equipment vendors to leverage their knowledge and expertise. A well-designed system will provide years of reliable service, but a poorly designed system can place a tank and the surrounding environment at considerable risk.