Most of today’s electric vehicles (EVs) rely on lithium-ion (Li-ion) batteries due to their high-energy density. As these batteries have become increasingly more advanced, so has the manufacturing process required to produce them—a complex interplay of chemical production and intricate assembly.
To meet the stringent production requirements, ensuring quality, safety, and reliability is paramount in the manufacturing of various components that make up the battery cell. The inherent variability of raw materials and the need for precise application of different gels, pastes, slurries, and liquid coatings make consistency across batches essential.
In an article published in Process Instrumentation magazine, Michael Machuca shares ways producers can leverage data from advanced measurement instrumentation and automation to manufacture high-quality Li-ion battery components at scale. He also covers strategies for optimizing the battery recycling process for successful resource recovery and waste reduction. The article focuses on three main chemical components of the battery: the cathode, anode, and electrolyte.
The anode is usually a copper foil coated with graphite, which is ground to a specific size, made into a slurry, applied to the copper and baked to bond, while maintaining conductivity and porosity. The cathode, more complex and variable by manufacturer, often comprises alloys like lithium-nickel-manganese-cobalt oxide or lithium-iron-phosphate, requiring high purity to avoid contamination. It is processed into a powder and applied to a metal foil. Electrolytes mix lithium salt, mainly lithium hexafluorophosphate, in an organic solvent, with additives to stabilize ion flow and protect the anode and cathode.
Monitoring Quality at Every Production Stage
Ensuring quality in batch manufacturing relies on recipe consistency and the precise measurement of ingredients. Achieving a high level of precision and addressing the variability in material properties and process conditions requires reliable data from measurement technologies. This includes:
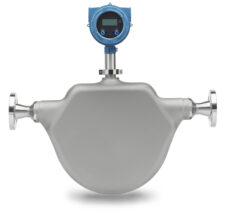
The Micro Motion™ ELITE™ Peak Performance Coriolis Flow and Density Meter delivers high precision and a wide turn-down ratio, making it an ideal choice for measuring liquids, slurries and gases.
- Mass flow and density meters. They provide direct mass flow measurement of liquids, slurries, and gases, crucial for accurate ingredient addition which is essential given the density variations.
- Monitoring and controlling pH levels using sensors is vital, especially when handling reactive materials.
- Viscosity control, critical for coatings or specific flow characteristics, can be achieved with instruments such as fork viscosity meters, enabling real-time adjustments.
- Conductivity measurements using toroidal conductivity sensors are critical for electrolyte quality control, directly indicating the electrolyte’s ability to facilitate ion flow.
- Non-contacting radar level transmitters to verify total batch volume, ensuring adherence to production specifications.
Ensuring Safety
The manufacturing of Lithium-ion cells involves highly reactive and hazardous materials, making safety a top priority.
- Facilities can utilize advanced toxic gas detectors, such as Emerson’s Rosemount 928 Wireless Gas Monitor and Rosemount 925FGD Fixed Gas Detector, for early detection of hazardous gas leaks.
- Flame detectors such as the Rosemount 975 Ultra Fast Ultraviolet Infrared Flame Detector are crucial for rapid detection of radiant energy.
- Enhancing process safety with the integration of safety-certified instruments compliant with IEC 61508 into safety-instrumented systems to prevent accidents, by closely monitoring pressure, temperature, flow, and level.
Improving Reliability
Intelligent process instrumentation also plays a key role in enhancing reliability through diagnostic capabilities that allow for proactive maintenance and better decision-making. This includes:
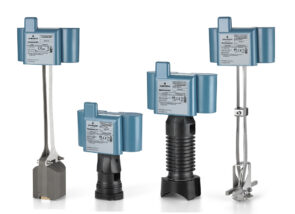
Corrosion and erosion can be continuously monitored via wireless ultrasonic thickness sensors that detect corrosive conditions and the actual loss of metal.
- Smart Meter Verification software, compatible with Emerson flow meters, provides real-time performance monitoring and historical data review.
- Continuous corrosion and erosion monitoring systems, such as the Rosemount Wireless Permasense ET410, provide real-time thickness measurements to ensure equipment integrity.
- Wireless devices and Bluetooth-enabled instrumentation offer flexibility by solving unique application challenges, such as mobile reactors that must be transported for cleaning after each batch. Wireless monitoring reduces the risk of damage and simplifies configuration and diagnostics, leading to cost savings.
Recycling Batteries
As EV batteries reach their end of life, recycling becomes critical for resource recovery and waste reduction. Many of the measurement instruments used in battery manufacturing, such as magnetic flow meters, pH sensors, and radar level transmitters, are also applicable to the challenges of battery recycling, including acid measurement in leaching processes and level monitoring in corrosive environments.
Read the article for more information on how data from advanced measurement and monitoring technologies are indispensable for successful EV battery manufacturing. By enabling precise quality control, ensuring robust safety measures, and improving equipment reliability, these sensors empower manufacturers to meet stringent product specifications and optimize resource utilization. Partnering with automation technology experts is crucial for organizations across the entire lithium value chain to achieve high-quality Li-ion battery production at scale.