Effective production of minuscule silicon chips requires water with close to zero impurities. This ultrapure water must be produced in a system made up of special components, including control valves with very specific features. The latter issue is the subject of my article in the July 2023 issue of Processing, titled “Control Valve Selection for Semiconductor Ultrapure Water Applications,” please find a summary below.
How silicon chips are made
Silicon chips are produced by layering materials and etching channels onto a raw silicon wafer. After each layer is processed, the wafer is polished flat with a mixture of chemicals, abrasives, and copious amounts of ultrapure water—1,500 gallons are needed to fabricate a 30cm wafer.
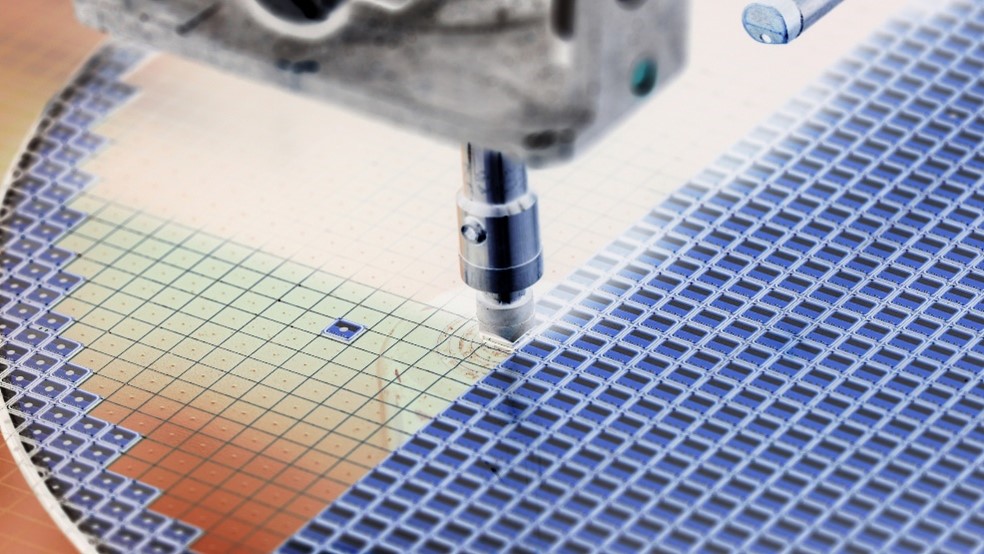
The silicon chip manufacturing process builds numerous chips layer by layer on a single wafer of silicon. Materials are deposited, carefully polished, selectively etched and covered with new materials in a multistep process.
Why ultrapure water?
Ultrapure water specifications far exceed those of water typically used in industrial facilities. These requirements are only growing tighter with each successive generation of chip miniaturization because smaller chip components are more sensitive to entrained particles and require lower levels of contamination.
Ultrapure water production usually begins with municipal drinking water, which undergoes complex processing to gradually remove impurities.
Given the vast quantities of water involved and the huge energy cost of processing, water purification and use is one of the major cost drivers of a semiconductor fabrication facility.
Preventing contamination
Once processed, ultrapure water must be kept free from contaminants.
Particulates can be introduced into the water from corrosive attack of the piping system, or by piping component degradation over time. Some bacteria can survive the ultrapure water purification process, and others may be introduced into the supply lines during maintenance activities.
For these reasons, the tanks, piping, and control valves that make up the ultrapure water system must be chosen very carefully.
Specialized valves
Control valves used in ultrapure water service must meet a set of requirements that go well beyond the norm for typical valves.
The material selection generally eliminates any graphite components as these can introduce particles into the water. It also ensures any wetted materials will resist attack from the water.
Minimizing surface roughness is critical to maintaining purity because smooth surfaces are easy to clean and offer no place for bacteria to establish a foothold. All wetted valve components must be carefully processed and electropolished to establish a smooth chromium oxide finish.
Furthermore, the surfaces require chemical passivation to remove rust-forming iron compounds. After passivation, valves are cleaned with a special agent in a dedicated cleanroom, and then specially packaged to prevent contamination during transport.
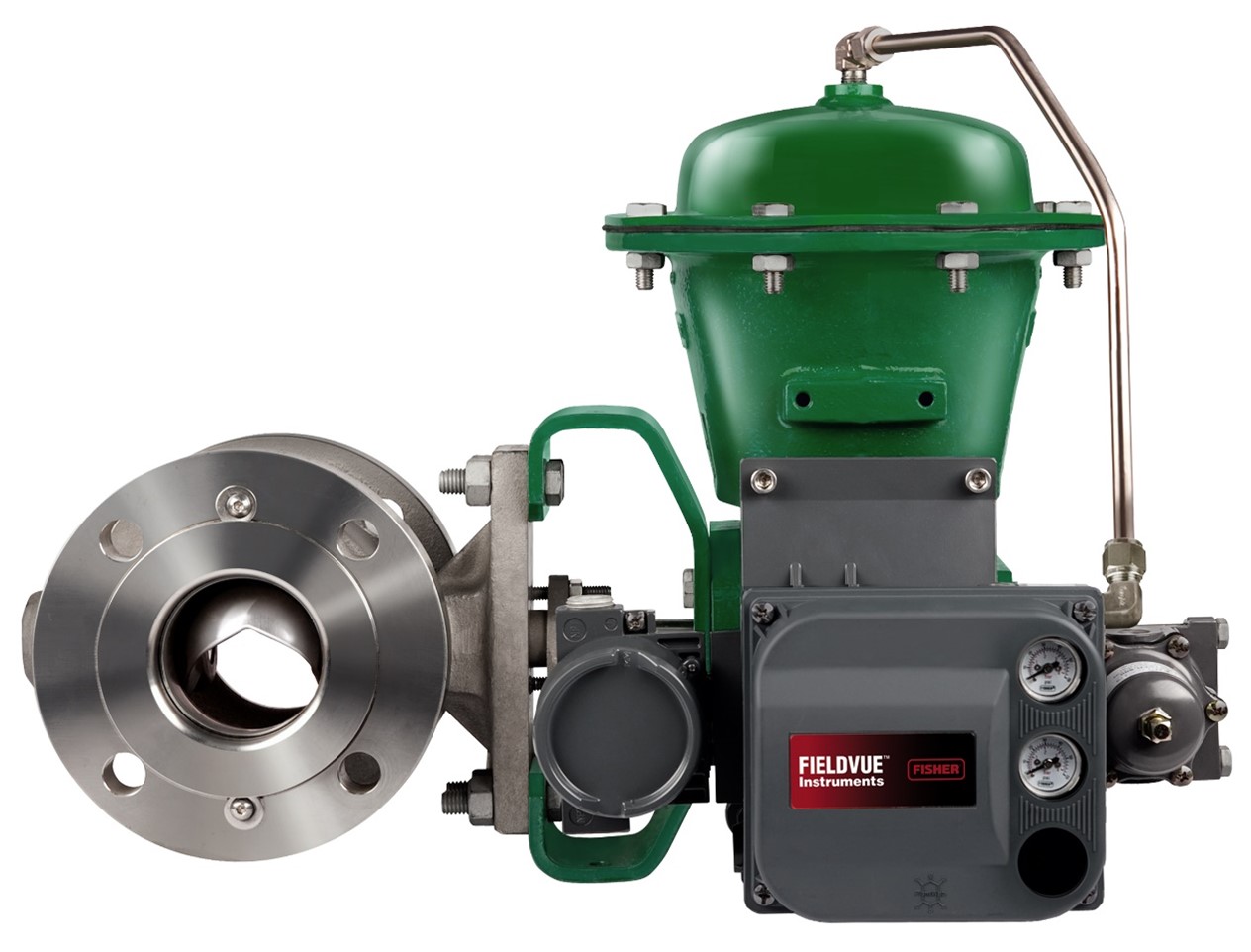
Control valves for ultrapure water applications (Fisher™ Vee-Ball™ V150) require numerous additional manufacturing steps and specialized fabrication protocols to meet semiconductor manufacturing specifications.
Such valves can be hard to find, but several manufacturers offer ultrapure water versions of their standard control valves in a wide range of flow sizes. Semiconductor producers should consult with their valve vendor during the selection process to learn about the options available for this specialty application.
Visit the Fisher™ Vee-Ball™ V150 webpage on Emerson.com to know more.