For chemical and specialty chemical manufacturers, reactors are used to perform many of the chemical reactions in the path to finished products. These reactors can be batch or continuously operated depending on the type of chemical reactions sought. In a World of Chemicals article, Improving Process Batch Performance in the Chemical Industry, Emerson’s Varshneya Sridharan shares considerations for effective reactor level measurement in both batch and continuous processes.
Varshneya opens highlighting the wide range of reactor operating conditions.
The process conditions in the reactor varies considerably. High temperature, high pressure and vacuum (Low pressure) are quite common in reaction processes and often tweaked for different states of the media (solids, liquids and gases) to make the product more efficient and economical. To be able to meet the diverse requirements of reaction vessels, sensors for level measurement must be able to cater to a wide range of application conditions.
He notes the importance of impellers in continuous reactors, where:
…one or more reactants, in solution or as a slurry, are introduced into a reactor equipped with an impeller (stirrer) and the products are removed continuously. The impeller stirs the reagents vigorously to ensure good mixing so that there is a uniform composition throughout. The flow rates are maintained at the inlet and outlets.
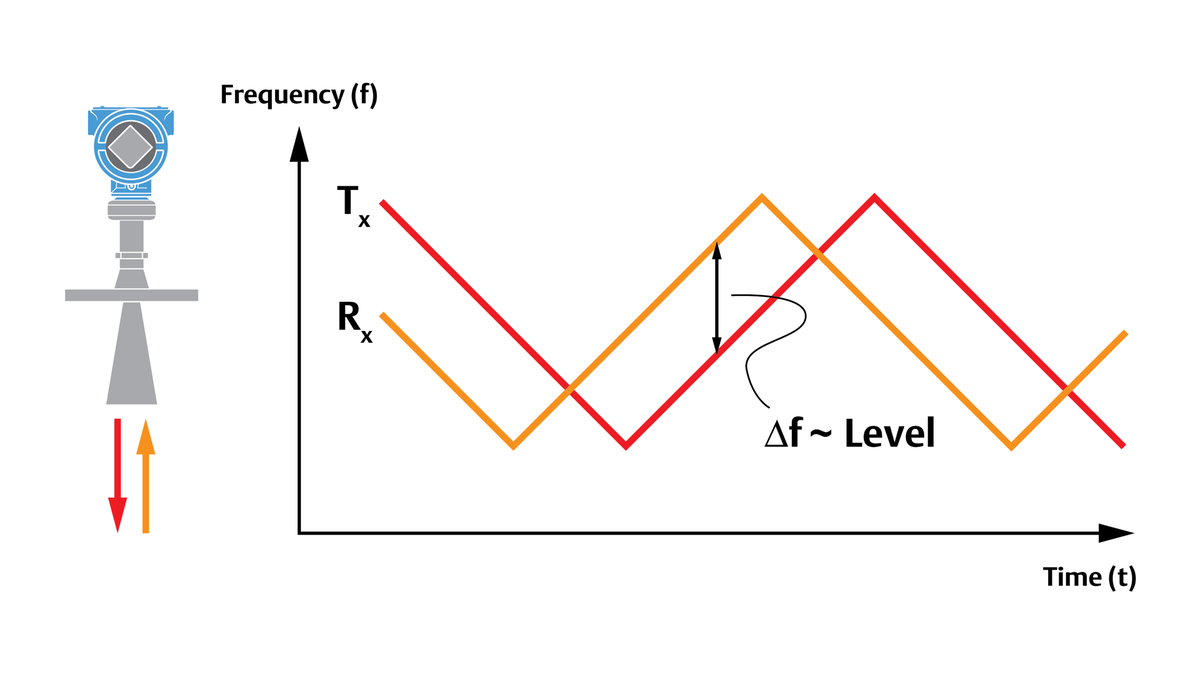
The 2-wire non-contacting radar Rosemount 5408 is optimized for best sensitivity in process applications. It uses fast-sweep Frequency Modulated Continuous Wave (FMCW) technology that deploys a continuous echo to maximize radar signal strength and produce a more robust and reliable measurement.
Impellers and other components found in vessels can be challenging for some level measurement technologies.
Nozzles, agitators and vacuum conditions posed complication for certain non-radar level measurement technologies including pressure-based solutions. With radar-based solutions, Emerson recommends Level Solutions using a combination of Continuous Level Measurement and Point Level Measurement for the purpose of providing best-in-class application solution.
For radar-based measurements, fast-sweep Frequency Modulated Continuous Wave (FMCW) technology found in the Rosemount 5408 non-contacting radar level measurement device, helps resolve challenges in vessels with these nozzles, agitators, vacuums, etc. by:
…accurately capturing echoes from agitator impeller and stable signal that is similar to other pulsed radar technologies or mechanical level devices. All the false echoes from the agitator impeller are registered and either masked or acted upon so that customers are not burdened with any false alarm.
Read the article for more on Varshneya’s perspectives on Rosemount 5408 operating ranges, installation, digital communication options, and how this technology helps improve operational performance. Visit the Rosemount 5408 Level Transmitter section on Emerson.com for more on this level measurement technology and case studies where it has been successfully applied.