The rapid development of the COVID-19 vaccine has created a dramatic shift in the way the public and life sciences organizations view the manufacturing of pharmaceuticals. In a recent Q&A with Pharma Manufacturing, Nathan Pettus, president of Emerson’s process systems and solutions business, shared how a move toward more flexibility and modularity in the industry is cutting tech transfer times to drive improved speed to market.
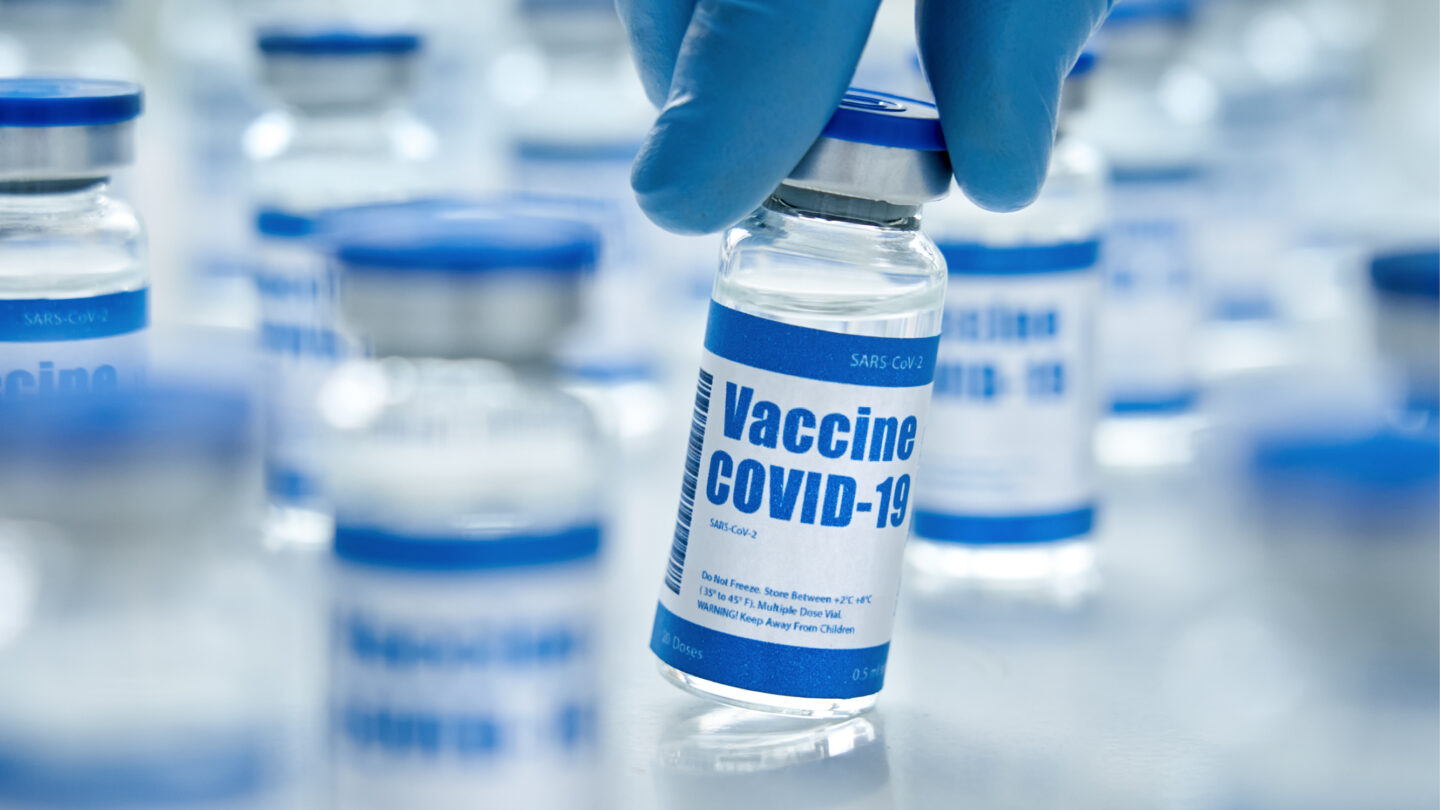
The development of the COVID-19 vaccine has had a dramatic impact on pharma production.
A more digital direction
At the heart of this increased speed and productivity is the digitalization of manufacturing techniques. The paper records and workflows of just a few short years ago have been pushed aside in favor of faster, more reliable digital solutions that also unlock improved collaboration. Nathan explains,
“If you can digitalize the process developed to make the drug, including its recipes, workflows, and scaling instructions, then you have a chance to automate the technology transfer to almost one click.”
Doing more with data
All this digital connectivity creates mountains of data teams can rely on to improve processes and identify problems before they cause production disruptions. That data must be collected, contextualized, and shared in order to be effective. Doing so takes time and effort but can yield impressive benefits, not the least of which is improved audit trails, as Nathan details,
“Data is the new gold. There is so much information involved in making a drug that from an information systems perspective, data is becoming increasingly important. Additionally, in the life sciences industry, the FDA requires that all processes be validated, and all data used be kept in records that are auditable and quality assured.”
Improvement is for everyone
It’s not only greenfield plants that are rolling out new digitalization strategies to improve technology transfer,
“Actually, the industry is forcing all of us to remodel both new and old facilities. You would think a greenfield project would be easy to design for the modular and agile trends, being that it is built from scratch, but the issue is you don’t really know how you are going to use that facility in two years. Leveraging existing equipment in a new way in a brownfield facility, built decades ago, is even harder.”
The solution, of course, is a new approach to design. New strategies and technologies are arriving to help make manufacturing more modular to automate the connection of equipment to a facility’s control and safety systems.
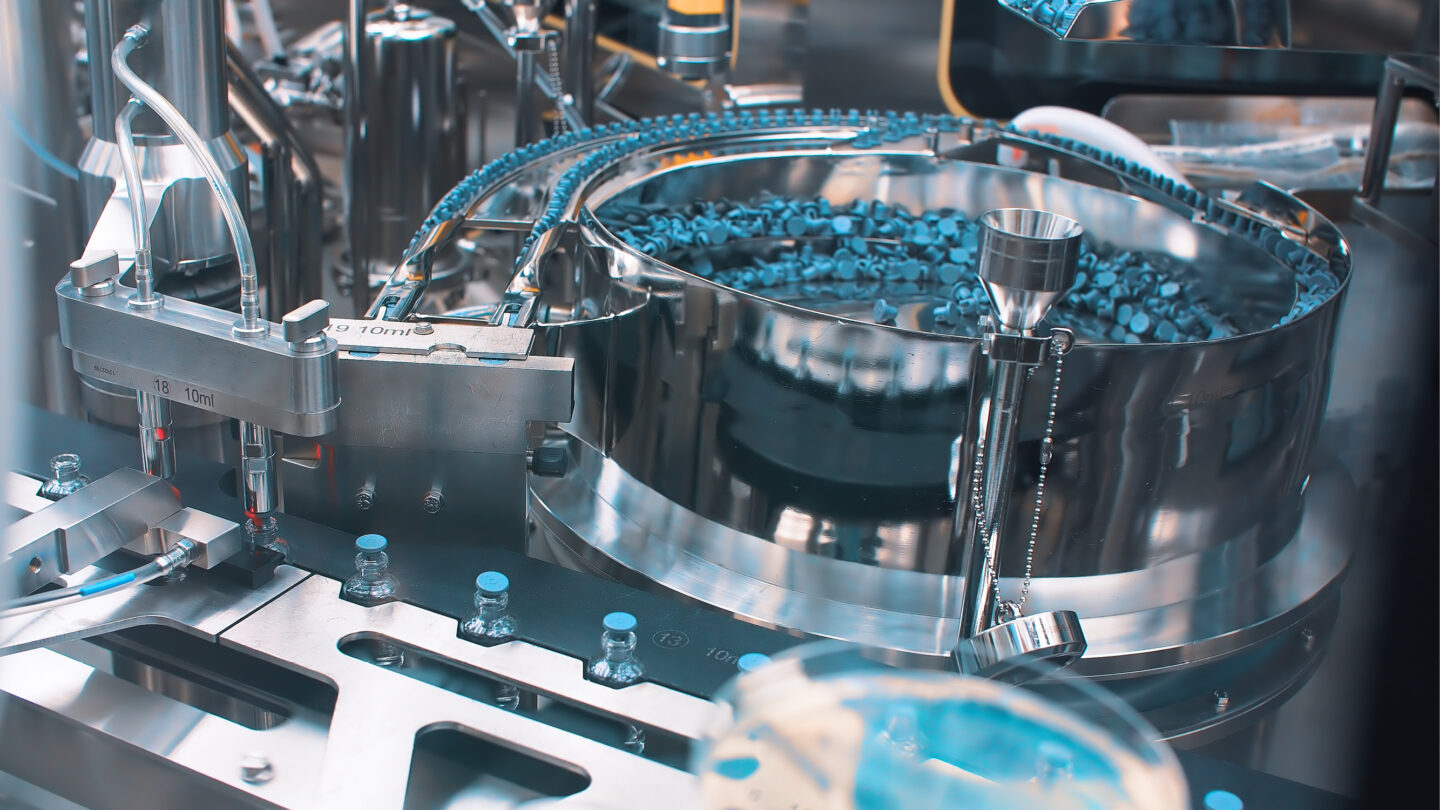
MTP has brought us the closest we’ve come to plug-and-play manufacturing.
Technologies such as Module Type Package are being leveraged alongside Emerson’s DeltaV™ Electronic Marshalling to make it fast and easy to connect or reconnect equipment. These technologies have brought new manufacturing equipment the closest to plug-and-play that it has ever been.
You can learn more about the way innovative manufacturing strategies are revolutionizing technology transfer by reading the article in its entirety. I’d also love to hear about how the strategies you use (no matter what industry you are in) have changed to improve speed to market. Feel free to share below!