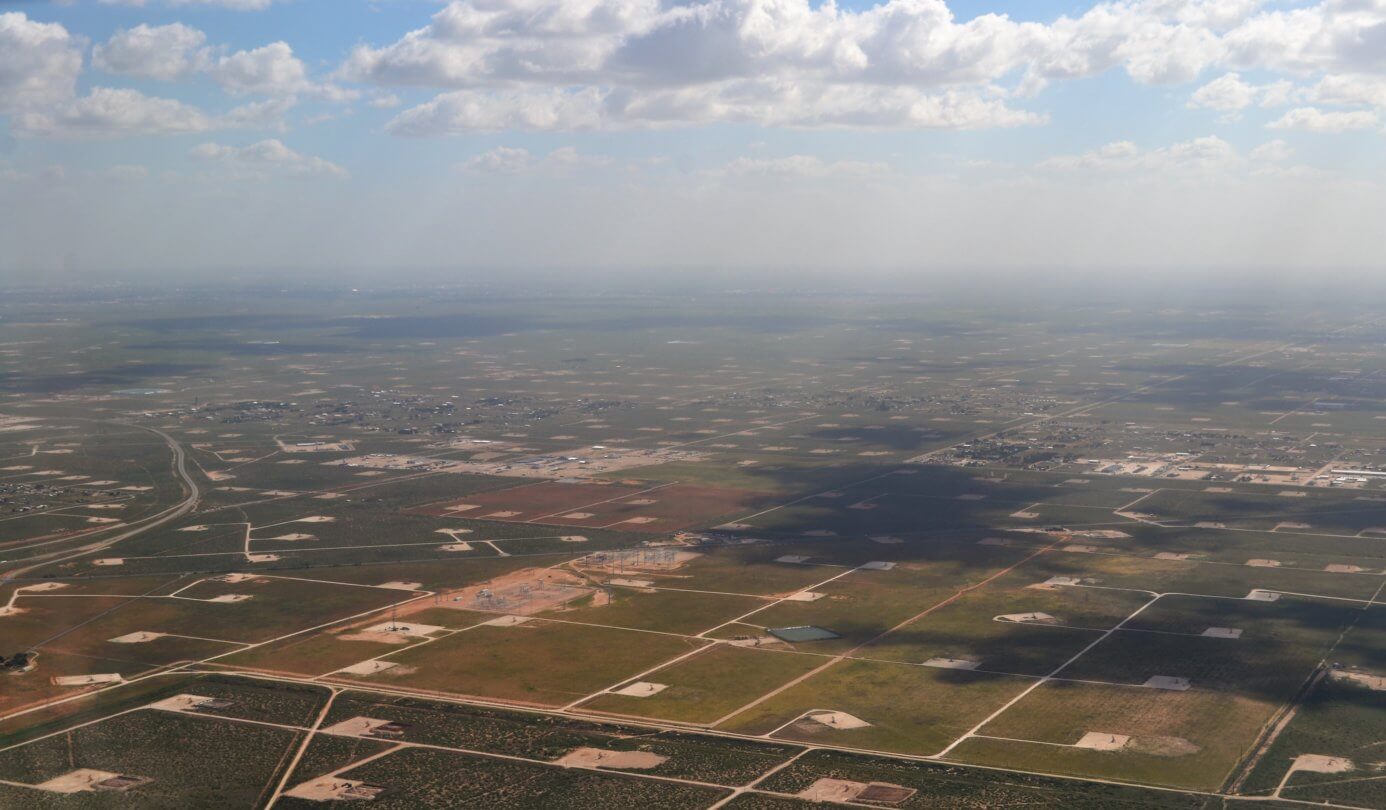
A birds eye view of the thousands of pumps, drills, and oil rigs connected by strings of dirt roads in the Permian Basin in Western Texas. An amazing sight with the clouds casting giant shadows and the bluest of skies above them.
In previous blogs we’ve taken a closer look at how our Roxar 2600 Multiphase Flow Meter (MPFM) performs compared to test separators in unconventional oil fields. Technology has advanced beyond the need for expensive and bulky legacy systems, and MPFM usage has been on the rise throughout the oil and gas industry since the early 90’s. Unconventional oil, in particular, is poised to benefit from groundbreaking strides in MPFM technology. Making the switch from one separator per well to one Roxar MPFM per well reduces facility capital investments at the well pad by over 50 percent. Let’s explore a few of the ways our compact Roxar 2600 MPFM makes this possible.
One-Size Fits Across the Life of the Well
At the beginning of the life of a well, the flow rates are high, requiring a larger sized solution for measuring and testing the flow rate. Over time, that initial surge dies off. If you are using a multiphase flow meter, then the size of the meter needs to change with the flow rates to stay in range. The Roxar 2600 MPFM utilizes field-replaceable venturi sleeves to adjust to these process changes. This easy-to-replace insert modifies the meter to handle these lower pressure flow rates, extending its service life and operating range. This sophisticated equipment ensures the meter has a one-size-fits-all range to cover your entire field.
While a test separator may function for the life of a well, the investment is so much greater. Due to that initial period of high production and, therefore, pressure, you end up purchasing a system sized to handle that pressure. As production rates reduce over time, you are not utilizing the test separator at its full capacity anymore. You’ve expended a significant amount of CAPEX to invest in a much larger version when you don’t actually need it for the long term.
Operational Ease of Use
Not only does this adaptability mean the MPFM functions throughout the life of the well, but it is also compact equipment that can be used over and over again across the field. Test separators are large systems with lots of pieces and moving parts. Transporting a test separator from one well to another requires an entire crew, heavy lifting equipment, and a driver with special permits to haul it where it needs to go. A lot can jostle around on those busy roads, so you need to perform a full inspection, cleaning, and maintenance after the move. With so many components and points of failure, this entire process takes a lot of time.
Compare this to the MPFM, which can be cleaned in 30-60 minutes and fully recommissioned within a 2-hour window. You’re achieving a much smoother transition well-to-well versus a test separator system. Additionally, this portability means the MPFM can be employed in periodic well testing too.
Less Land, Less Mess, Less Maintenance
With the Roxar 2600 MPFM, less really is more. That’s what we mean when we say it takes up a much smaller footprint than legacy equipment. When a test separator is installed, the land is torn up to add the extra line for the separator system. When an MPFM is installed directly at the wellhead instead, the additional pipeline is not needed. This creates considerable savings by cutting out the work of installing that extra pipeline and the space it would have required.
A well pad is situated on land leased by the square foot. By cutting out the footprint needed for a test separator, you aren’t leasing as much land for your well pad. You’re saving on the costs of maintenance required to perform on the property you lease as well. Also, depending on your lease, you might be obligated to return the land to its natural state once your contract has expired.
Multiphase flow meters also have fewer connections and a much lower chance of leakage than separators. Fewer potential leaks and oil spillage on a smaller footprint mean less upheaval overall and substantial safety and environmental benefits. In areas like Colorado and Wyoming, where it takes decades for vegetation to grow, less ground disturbance is a significant advantage. Anytime you can avoid tearing up the soil is positive from an environmental and cost perspective.
Furthermore, there are significantly fewer points of failure on an MPFM and no moving parts, which improves the safety of operation and reduces the potential for leaks.
Overall, this new application of proven technology has significant advantages over legacy equipment. If you’ve made the switch to MPFMs please share some of the ways you’ve seen MPFMs improve operations. Comment below or visit Emerson.com/RoxarShale.