The growing need for experience and rapidly advancing high-bandwidth communications technology is driving new thinking among process manufacturers on how they manage their operations.
The authors of the book, Integrated Operations in the Oil and Gas Industry noted:
Over the last ten years integrated operations [IO or iOps] have gone from initiatives started by enthusiasts, through pilot testing and broad implementation of new IO practices.
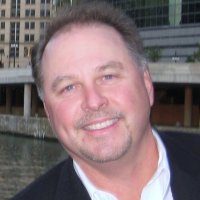
Jeff Dymond
Oil & Gas Industry Solutions Director
He notes other trends beyond experience gaps including increasingly complex manufacturing and production processes and increasing data flows—alarms for operations and work orders for maintenance personnel. It’s critical to turn the flood of data into actionable information. It’s also important to unlock information siloed in departments around the organization
Jeff describes the origins of iOps [hyperlink added]:
The term originated in the petroleum industry, where it referred to the movement of operations, maintenance and production functions from offshore platforms that were connected by broadband links for videoconferencing and data sharing to iOps command centers on shore. The Center for Integrated Operations in the Petroleum Industry (IO Center)—an industry consortium dedicated to these concepts—defines iOps as “the integration of people, organizations, work processes and information technology to make smarter decisions. It is enabled by global access to real-time information; collaborative technology; and integration of multiple experts across disciplines, organizations and geographical locations.”
iOps have spread to many segments of the process industries including oil & gas production, refining, chemical, power, life sciences, and mining. It’s implementation:
…takes the form of an iOps command center, in which people in the local plant can meet and exchange ideas by videoconference—not just with a regional center but with an asset support center, global company experts, external experts, and vendors and partners.
Jeff explains the various roles interaction in an iOps environment:
Engineering support can be readily supplied to a facility anywhere in the world directly to and from an iOps command center. Personnel can remotely consult on operations. Remote monitoring and diagnostics gives experts the ability to connect from around the world to process control devices and equipment such as analyzers, flowmeters, automated valves, pumps, motors, compressors, turbines and electrical equipment to diagnose and solve problems. The collective knowledge of experienced operators can be entered into databases and shared with people in all company facilities, wherever they are located.
Two key technologies to foster this collaboration include wideband communications and pervasive sensing. Wideband communications foster virtual face-to-face meetings among widely geographically dispersed experts. Pervasive sensing:
…the installation of networks of intelligent (and frequently wireless) field sensing devices—which provides process and equipment health data not only to process control and safety systems but also to applications and business systems throughout the enterprise.
Using these technologies, an iOps command center has five basic attributes:
- Remote operations and remote monitoring: This allows operators and engineers to monitor and/or control a remote facility, improve process control, and diagnose and solve problems at a site;
- Integrated/centralized maintenance: Maintenance applications integrated with work processes, possibly including centralizing and dispatching maintenance personnel, allows a higher degree of integrated planning, leading to optimized maintenance plans and budgets;
- Collaboration: This allows maintenance, production and business personnel to collaborate with experts at other locations or at any business unit throughout the enterprise;
- Production planning and optimization: This allows personnel to plan and optimize production at particular facilities and across the enterprise; and
- Business operations: This allows personnel to perform operational risk management, production accounting, enterprise performance management and other tasks.
Each area can add business value and process manufacturers may focus on the ones that create the most value and provide a path for increased iOps scope over time.
Jeff closes noting how better decisions and quicker responses can lead to increased business opportunities, streamlined, more efficient business processes, and greater connection of:
…subject matter experts inside and outside the company benefit greatly by having instant, real-time validated data to make informed decisions to solve problems on critical assets like turbo-machinery or to debottleneck a complex process.
Read the full article for ideas on how your organization might benefit from integrated operations and connect with Jeff.