Improving heat rate is something that most power generators consistently look to do because it translates directly into lower fuel costs. In India, there are government legislated heat rate targets for plants where financial penalties or rewards are available depending on which side of the equation a plant lands.
As most know, there are many ways to go about improving heat rate. These range from large capital projects that focus on mechanical changes to smaller control and automation upgrades. Focusing on feedwater heaters is one place where heat rate gains can be made.
The purpose of a feedwater heater is to improve overall plant efficiency by drawing a bit steam from the turbine and use it to preheat boiler feedwater. Although there is some energy lost in the turbine cycle, the overall plant impact is a net gain in heat rate.
Good controlling of the condensate level in this process is needed to maximize heat transfer, and at steady state conditions, most technologies are adequate for this process. However, with more and more plants cycling load, there are errors introduced into the process from changing water densities that makes controlling level more difficult.
Higher condensate levels can lead to turbine water induction while lower levels can cause flashing in the drain cooler. In either case, mechanical damage is often the result. Another effect at lower levels is that heat transfer suffers which requires more firing in the boiler to add more temperature to the process.
Although density compensation can be done in plant controls, the system is not always reflective of actual conditions in the heater. At higher temperatures where the dielectric constants of water and vapor become too close to differentiate, dynamic compensation should not be used.
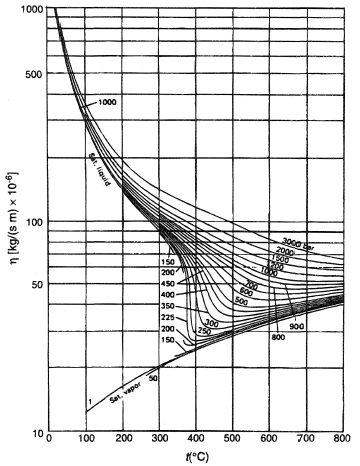
Source: Themopedia: Steam Table
A better approach is to apply a technology that can overcome the effects of dielectric constant convergence at higher temperatures.
The bottom line is that by using this technology you can more accurately control the heater vessel level so you can maximize heat rate while avoiding mechanical damage from condensate level being too high or too low.
From Jim: You can connect and interact with other power and level experts in the Power and Level groups in the Emerson Exchange 365 community.